Maintenance
The information listed is for services in Japan and may vary depending on the region where the service is available.
Please contact us for details.
Don’t you have any requests like this?
[Spot]Maintenance service
- I have a little problem with the machine recently, so I want you to see it once.
- I would like to relocate the machine, but I would like to have it set down, set up, etc.
- Have troubleshooting urgently
[Periodic inspection]Maintenance services
- I would like to have a periodic inspection.
- Have machine diagnostics to maintain production capacity
- Preventive maintenance
- I want to increase productivity.
[Spot] Maintenance service
JUKI accepts call
Immediately responds to any trouble with reliable support.
Feature
1.Worldwide support
Smooth response to movement of production sites
Rapid response to parts supply by local staff
2.Remote maintenance is also possible.
Detailed maintenance service support is available even in remote locations where business trips are difficult.
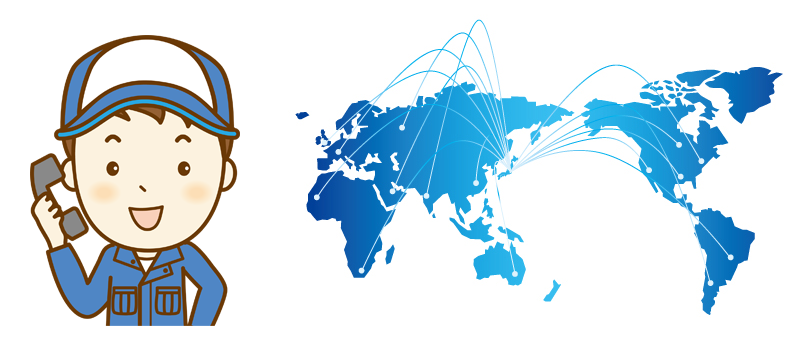
Remote support image
Machine trouble at customer factory
JUKI accepts call
Customers |
Operate in front of the machine![]() |
JUKI | ||
Previously operating the PC on the same screen as the customer | Advice on Smart Glass | |
![]() |
Solved!
Contents of service
- Emergency troubleshooting
- Facility relocation
- Consultation on other equipment
[Periodic inspection] Maintenance services
For more stable production…
We recommend periodic inspection (machine diagnosis) every six months by the manufacturer’s service personnel.
Service contents of periodic inspection
- Software cleanup
- Cleaning the hardware
- Shaft, shaft grease, oil up
- Replacing recommended consumables
- Verifying and upgrading the software by JUKI
Effectiveness of periodic inspection
- Various clean-ups reduce the consumption of parts
- Replacement of consumables and recommended parts enables maintenance of production capacity
- Revision management keeps track of machine status at all times
- Improved productivity by keeping the machine up-to-date